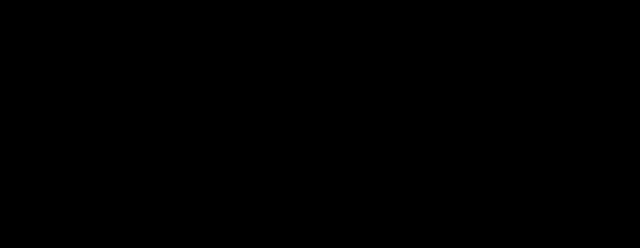
The next step in McLAREN's use of sustainable composites in F1
McLaren goes racing with Bcomp
Read time: 17.5 minutes
- Natural fibre composite seat raced for the first time at the 2021 British Grand Prix
- Lifecycle analysis reveals the seat has 85% lower CO2 emissions
- Daniel Ricciardo’s seat features hybrid sandwich construction of flax and carbon fibre
- New timing stand and engineers’ island made from natural fibre composites to achieve 3,450kg reduction in travelling freight weight
The 2021 British Grand Prix saw many firsts: the first Formula 1 event with a capacity crowd since the covid-19 pandemic began; the first McLaren driver to score points in 15 consecutive races; and the first grand prix in which a natural fibre composite seat was raced. Lighter, cheaper, safer and more sustainable, in 2020 we revealed how we worked with Swiss sustainable lightweighting specialist Bcomp to develop F1’s first natural fibre racing seat. A year later, the seat was finally raced in anger at the British Grand Prix, but just what have we learnt about sustainable composites in that time and how are we now using them off the car as well as on it?
Shrinking our carbon footprint and eliminating single-use plastic
For starters, the environmental impact of the seat is an area where we’ve furthered our understanding over the past year. “Together with McLaren, we analysed the sustainability of the seat,” says Bcomp CEO and Co-Founder Christian Fischer. “In Lando Norris’ seat we can make use of all the sustainability and performance benefits of ampliTex™ and powerRibs™, resulting in 85% lower CO2 emissions. That means, even when taking into account the emissions in raw material production and manufacturing processes of the part, we can reduce the vast majority of the seat’s footprint by replacing all carbon fibre plies with an optimised ampliTex™ and powerRibs™ flax natural fibre layup. If Lando’s seat needs to be replaced, since it is all natural fibre, it can be used for thermal energy recovery, turning approximately 80% of the energy stored in the seat into renewable energy.”
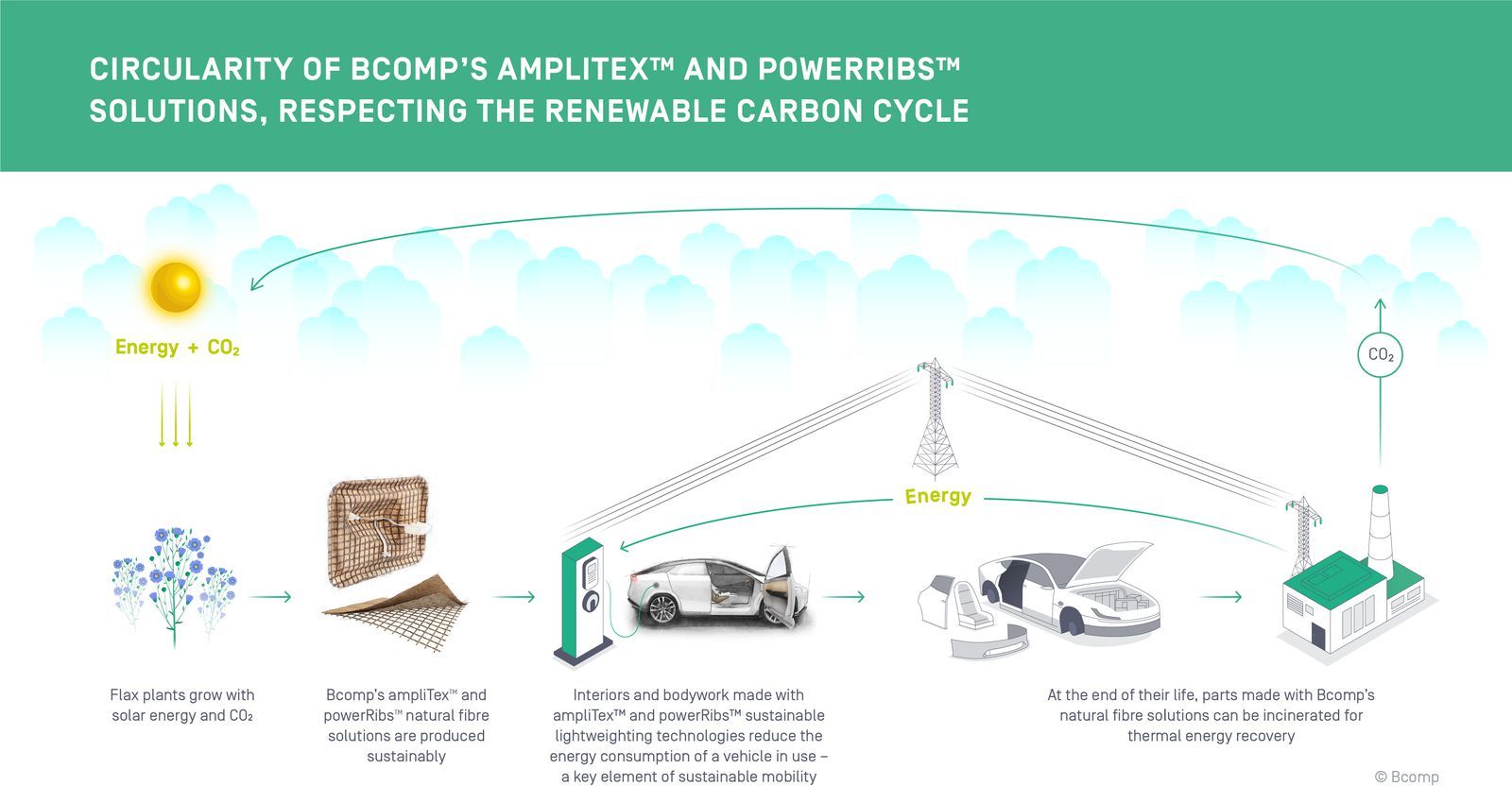
The benefits don’t stop there. As part of our commitment to being a sustainable team, at McLaren we’re aiming to eliminate single-use plastic from our operations and the use of powerRibs™ technology in Lando’s seat is an example of this. “By putting the powerRibs™ over the surface of the underlying structure that has resin in it, you get an even distribution of the vacuum within the bag during the autoclave process without the need for a plastic breather,” explains McLaren F1 Composite Design and Technology Engineer Steve Foster.
“Approximately 340g of single-use plastic per square metre is used as a breather in the production of a carbon fibre part, but the powerRibs™ eliminate the need for this. That’s not all, the breather is a soft, duvet-like material that tends to smooth out the edges of the part. This makes it harder to get a sharp finish with well-defined edges, but without the breather you don’t have this problem.”
Same, but different
After a year of testing and development, you’d think that the seat we raced at Silverstone might have evolved significantly from the original. Truth be told, however, not much has changed besides “a bit of additional padding here and there,” according to McLaren F1 Design Engineer Scott Bain. “The chassis didn’t change over the winter break and neither did Lando, so the seat he raced in is from the same mould we used to make the original. The reason it’s taken longer than we would have liked to race with the seat is that there’s always a degree of cautiousness around bringing highly experimental components to the car.
“Last year, the covid-19 pandemic meant there was a lot of uncertainty around when and where we would race, which made it very difficult to plan when we could run without disrupting our race weekend plans or Lando. And it’s been difficult this year because we’ve lost an hour of free practice – and even more time when there’s sprint qualifying.
“The lack of time forces you to commit to running something like a new seat from the outset of a weekend because the last thing you want in a one-hour practice session is to be playing around with the seat. If the driver isn’t comfortable it can affect their confidence, which ultimately hinders their ability to extract the maximum performance from themselves and the car. That’s something we’re very conscious of, especially with Lando performing as well as he has been. We didn’t want to change anything that might throw him off.”
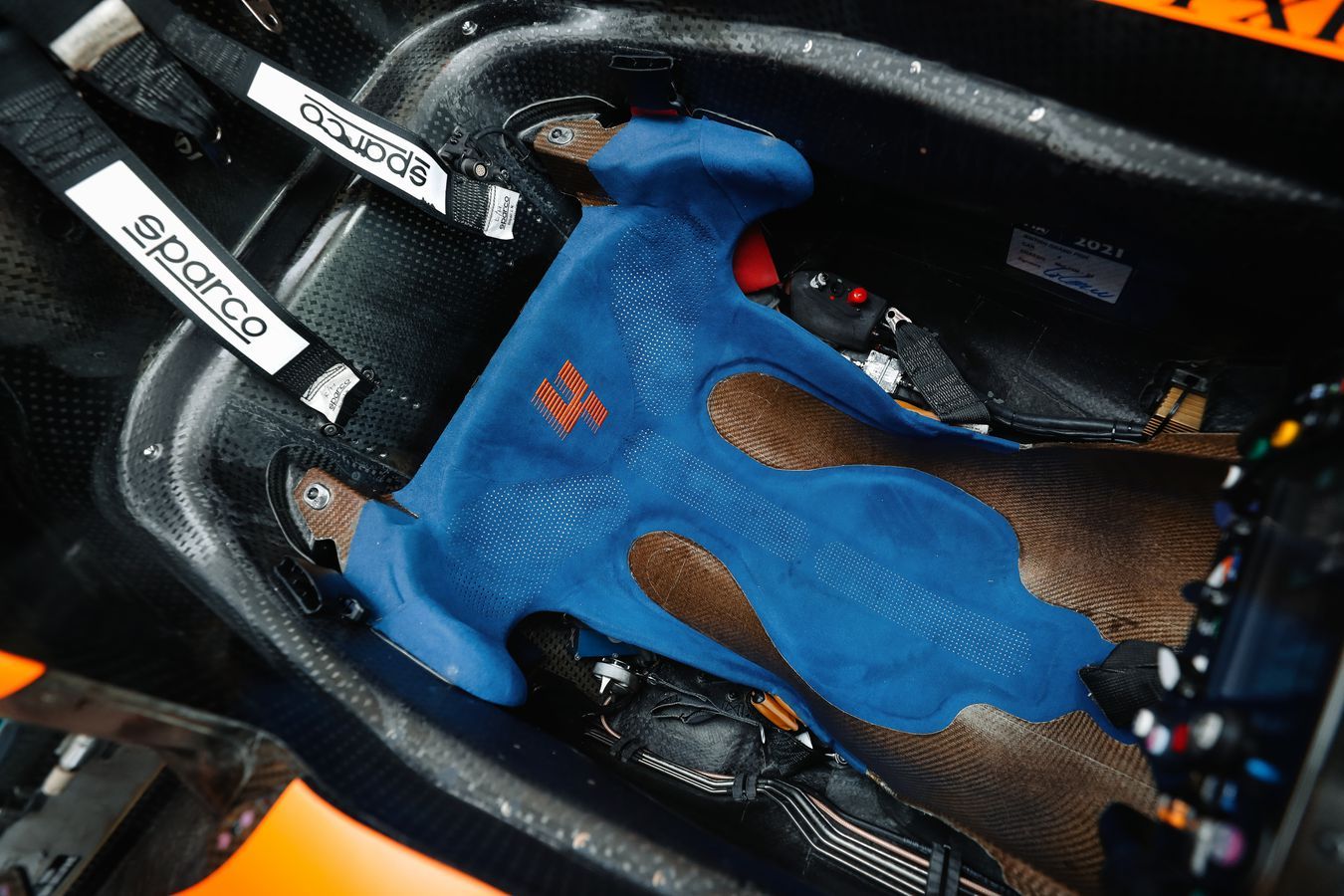
But, by all accounts, much to the relief of Scott and the team, Lando hasn’t had to adjust to life with the natural fibre seat. “After running it in free practice for Austrian Grand Prix and throughout the British Grand Prix, Lando didn’t have any feedback on the seat other than he was happy to continue using it for the rest of the season,” says Scott.
“It might sound strange but, in this instance, no feedback is actually a good thing. As far as Lando is concerned, nothing has changed at all, it’s as if he’s still using the same old carbon fibre seat. But, as we all know, the seat he’s using now is very different when you consider the material it’s made from and the cost and environmental benefits that brings.”
More than meets the eye
So that’s Lando’s side of the garage, but what about Daniel Ricciardo’s? A different driver invariably means a different seat. In F1, each seat is bespoke to the driver, moulded to contours of their body, and with Daniel joining McLaren at the start of 2021 the team had to make a new seat for him. “Because Daniel was new to the team, he was an unknown quantity, we didn’t know exactly what he wanted from his seat, so we felt the safest bet was to stick with carbon fibre to reduce the chance of any problems,” reveals Scott.
The Aussie is also slightly heavier than Lando, which meant he required a lighter seat. This limited the amount of additional bio-composite material we could use to ensure his seat had the required levels of strength and stiffness – as we had done with Lando’s. Keen to take advantage of the benefits of using natural fibre material, such as greater vibration absorption and comfort, reduced cost and lower carbon footprint, we opted for a hybrid sandwich construction of flax and carbon fibre.
Daniel’s seat has the same level of strength and stiffness as Lando’s seat, it’s just achieved in a slightly different way. Where Lando’s seat relies on Bcomp’s powerRibs™ technology – a thick yarn formed from twisted flax fibres – to provide a three-dimensional grid structure that reinforces Bcomp’s woven flax fibre reinforcement fabric, ampliTex™, Daniel’s features a layer of ampliTex™ sandwiched between two layers of carbon fibre.
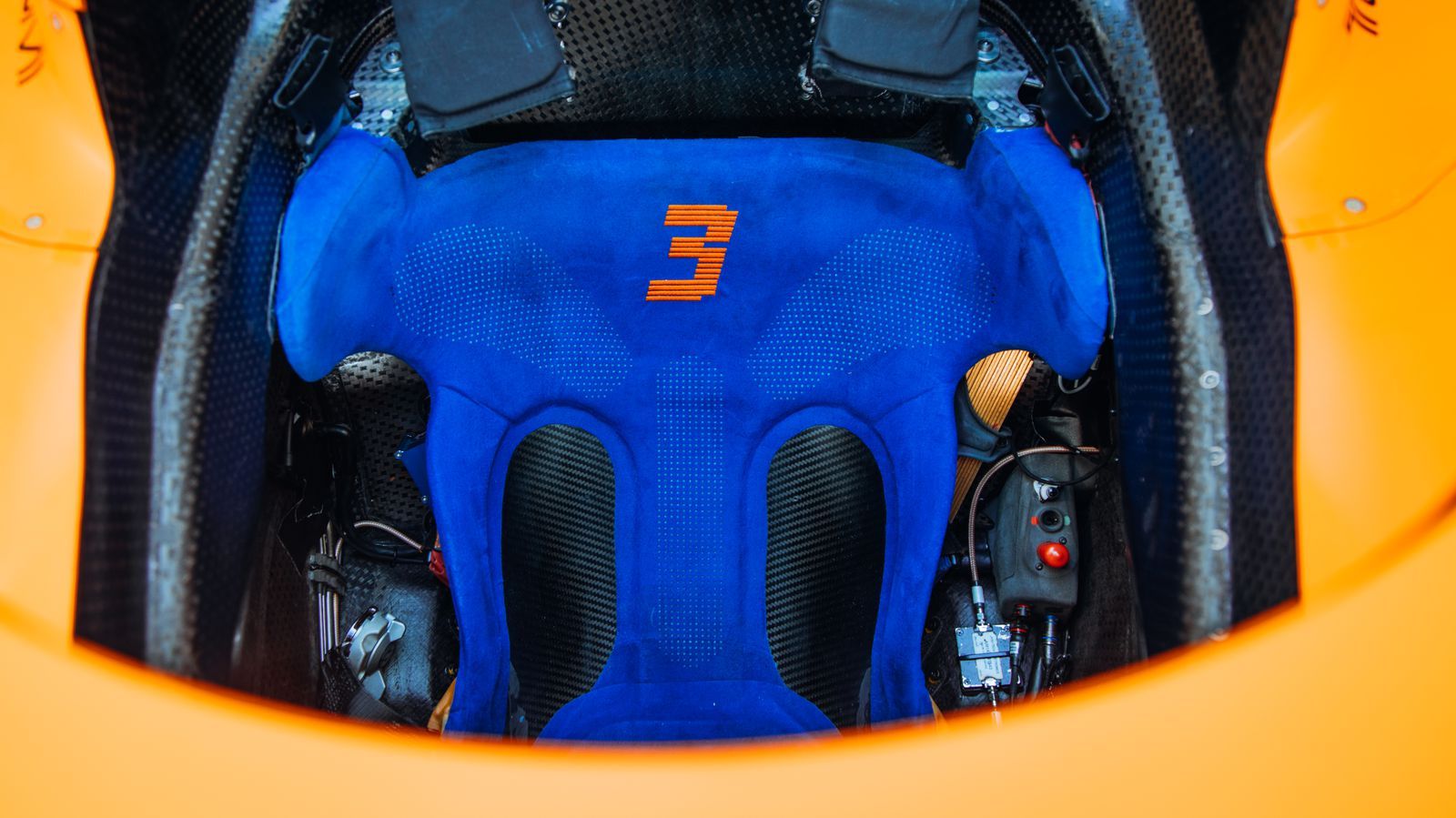
You wouldn’t think it looking at it, but the majority of Daniel’s seat is flax, it’s just hidden beneath skins of carbon fibre. To the naked eye, it looks the same as any other race seat on the grid – except Lando’s, of course – and yet, “Using ampliTex™ to replace part of the carbon fibre plies in Daniel’s seat still reduces emissions by 28% and improves the vibration damping of the seat,” reveals Christian.
“By separating the carbon fibre skins in the seat, the ampliTex™ is essentially enabling them to work much harder,” explains Steve. “The flax filling in this ‘sandwich’ construction plays an important role by transferring load between the inner and outer carbon skins and providing compressive strength through the thickness of the sandwich. It doesn’t need to be super strong and stiff itself to do this job, but by being much stronger than ‘normal’ core materials such as foams or honeycombs, it adds significant durability in ‘hardpoint’ areas – where the seat is supported in the cockpit and where it has to resist the highest stresses from cornering and grounding, for example. A solid carbon fibre construction would do the same job but would be unnecessarily expensive and take much longer to manufacture, aside from the additional environmental impact.”
“In fact, even after driving the car, Daniel didn’t realise there was flax in his seat until we told him,” says Scott. “Again, it’s a bit like Lando not having anything to say about his seat: no news is good news. If it’s not affecting the driver’s comfort and confidence, that’s a big tick. It also confirmed for us that a hybrid construction was a way in which we could incorporate natural fibre composites into structural components of the car.”
“Daniel’s seat is a great example of how you can use natural fibre composites intelligently,” adds Steve. “We’re able to achieve the strength and stiffness we need for this safety-critical component, but we’re still minimising the amount of carbon fibre we’re using. “The approach is no different to when we make the chassis of an F1 car, which features a lightweight aluminium honeycomb core with relatively thin skins of carbon fibre on either side. You end up using significantly less carbon but achieve the same strength and stiffness as if you had used a thick, solid laminate.”
Going further with natural fibre composites
When we began working with Bcomp, we weren’t only looking to apply natural fibre composite technology to the car. We were keen to go further and explore where flax fibres could be used intelligently off the car to reduce weight and cost while maintaining and, in some cases, improving performance. This season has seen our first off-car development come to fruition. From the start of the campaign, as part of our continued effort to reduce material costs and boost the sustainability of our operations, we introduced a new timing stand and engineers’ island that features a hybrid sandwich construction of flax and carbon, very similar to that of Daniel’s seat.
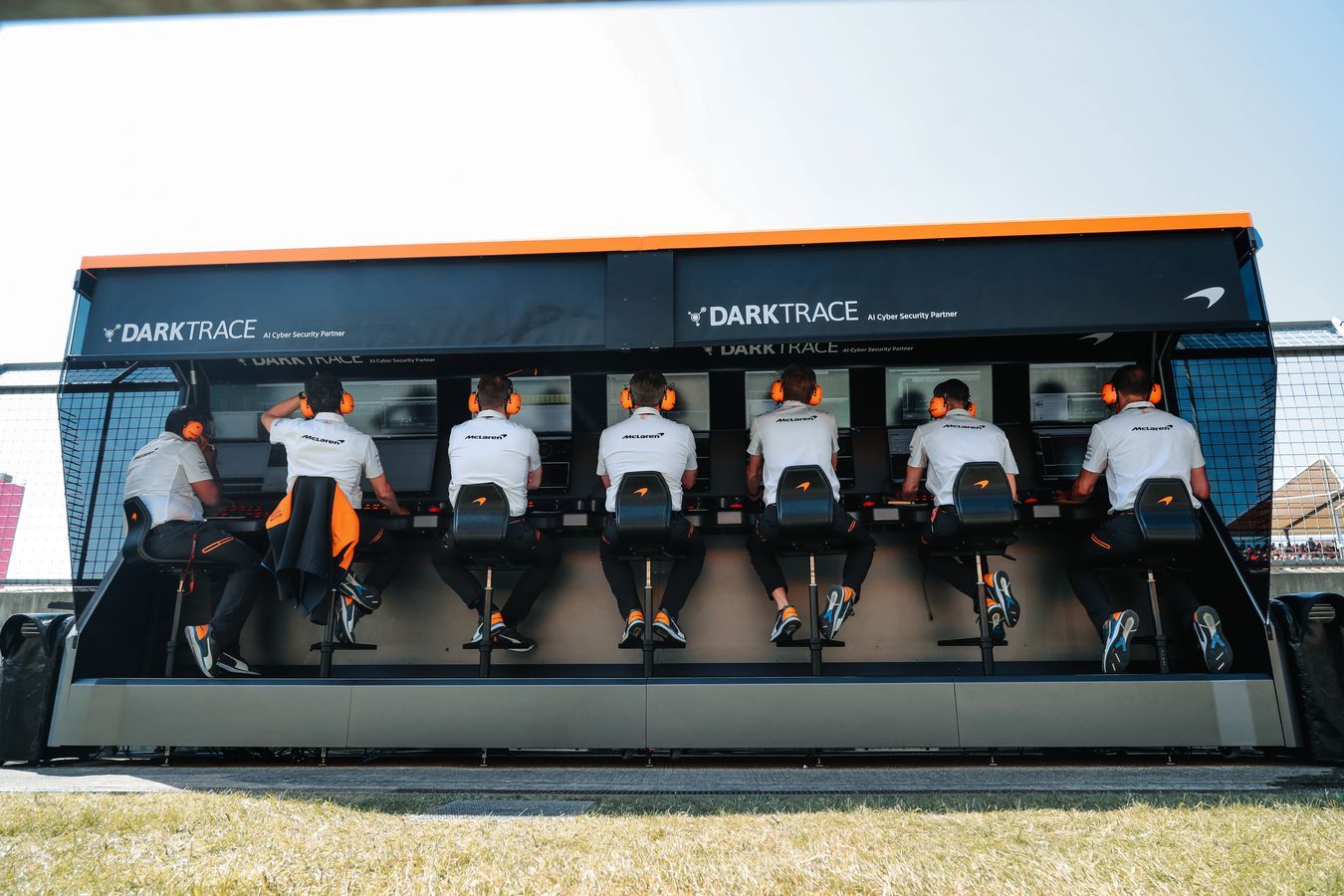
For those wondering what the timing stand is, it’s commonly referred to as the ‘pit-wall’ and is usually located opposite the garage. During a race, it’s where you’ll find members of team leadership and our race engineers. Meanwhile, the engineers’ island sits between the cars in the garage and serves as the main hub for engineers during a session, providing them with a direct link to the drivers, mechanics and rest of the team, as well as a wealth of data.
“The new timing stand and engineers’ island are two-thirds flax and one-third carbon fibre,” reveals Steve. “We could have made them entirely out of flax but, in our effort to minimise waste, we chose to use carbon fibre that was about to go out of date. The carbon fibre we use is pre-impregnated with a semi-liquid resin polymer, or plastic. During the manufacturing process it is placed into a mould and then cooked at high pressure and temperature in an autoclave, turning it into a solid part. But, because the resin is activated from the point of manufacture the curing process is already underway, albeit very slowly. We store the pre-preg carbon fibre in a freezer to slow this process down and maximise its shelf life, but after around a year it will be at the end of its ‘life’ and unusable for major structural car parts.
“Having the right amount of carbon fibre in stock is a bit of a balancing act. In an ideal world, you wouldn’t have any surplus stock, but you always order more than you’ll need so you’re covered in terms of car development. You never want to be in a situation where a new part comes along, but you can’t make it because you’ve run out of carbon fibre. Inevitably, you end up with surplus stock, but we look to minimise waste by using it in applications such as the timing stand and engineers’ island.”
Previously, the team had just one timing stand and engineers’ island made entirely of carbon fibre, which was transported around the world via air freight. However, by using such a high percentage of flax in the new design, it was cheaper to make five sets of the new timing stand and engineers’ island and transport them via sea freight, decreasing our amount of air freight and reducing our carbon footprint as we travel around the globe. It’s meant that, in conjunction with the introduction of a new overhead lighting system for the garage, which also houses the power supply to the cars and equipment, the team has been able to reduce its travelling freight by 3,450kg.
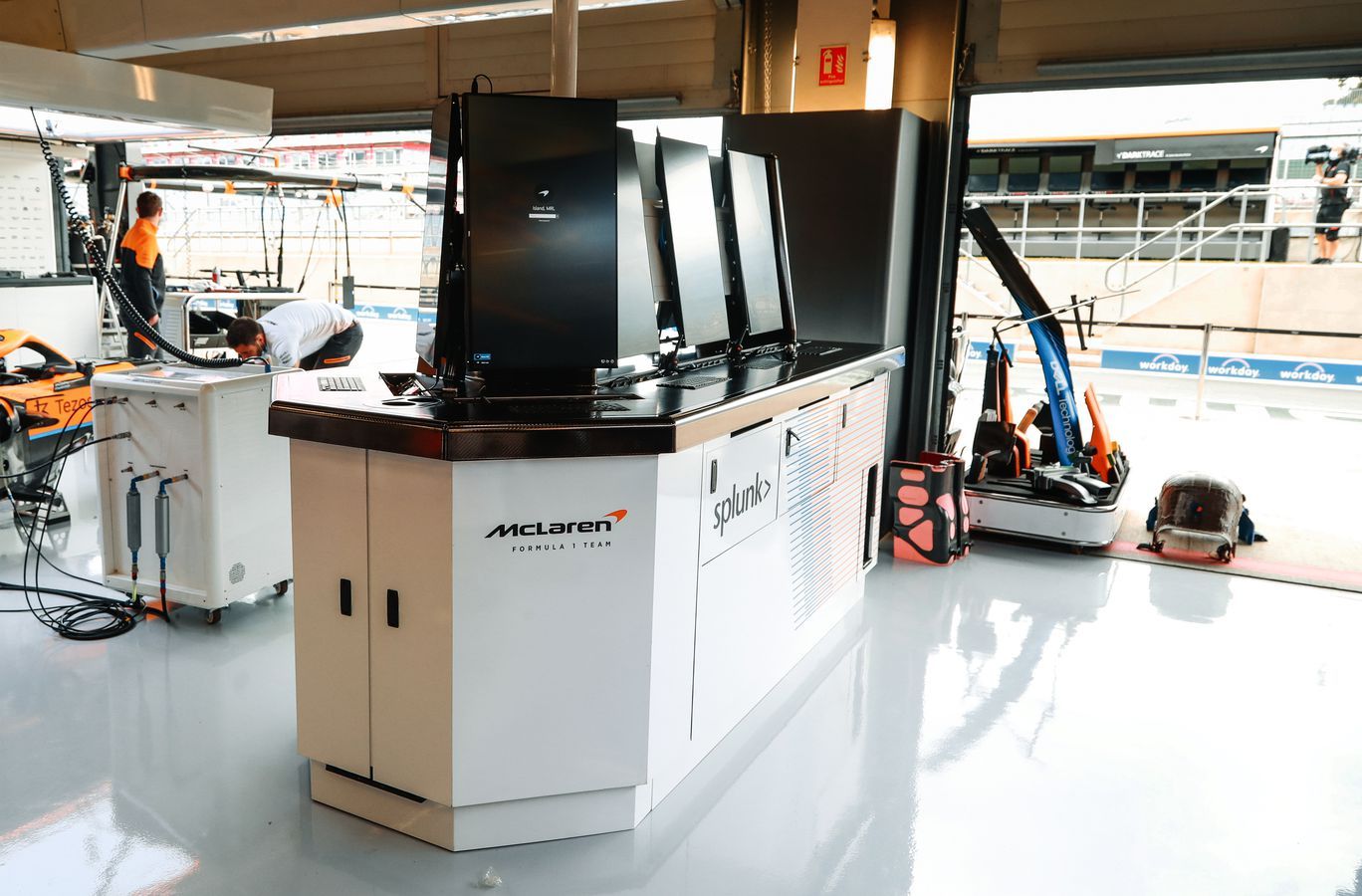
Every day is a school day
“Our understanding of natural fibre composites has grown considerably since we began working with Bcomp last year,” says Steve. “As we’ve developed Lando’s seat, then implemented the hybrid sandwich construction in Daniel’s seat, and begun to introduce the technology off-car with the timing stand and engineers’ island, we’ve learnt a lot more about natural fibre composites: the way they handle; the way they cure; their strengths; their weaknesses; and how they can be used with other materials.
“All this knowledge is constantly being fed back into the team and opening up avenues, both on and off the car, for further applications that can deliver competitive advantage and sustainable innovation. It’s been a steep learning curve but it’s hugely exciting to be working with a technology that is a cheaper, high-performing and, crucially, sustainable alternative to carbon fibre. We’ve made good steps forward with the racing seats, the timing stand and the engineers’ island, but we’re not stopping there. There’s more to come.”
“The use of natural fibre composites is not only a pioneering innovation in the best traditions of McLaren Racing, but directly contributes to our sustainability commitments through the ingenuity of our people and our supply chain,” says McLaren Racing Chief Communications & Sustainability Officer Tim Bampton. “Specifically, it addresses our two overarching environmental goals, namely becoming carbon net zero by 2030, and our transition to the circular economy through the elimination of waste, reuse and recycling. This exciting development illustrates the great potential for more sustainable innovations in the future.”
Join the team
McLaren Plus is our free-to-join fan loyalty programme, bringing McLaren fans closer to the team with the most inclusive, rewarding and open-to-all fan programmes in F1 & esports.
Sign up now, or current members can amend their details in the form below if necessary.