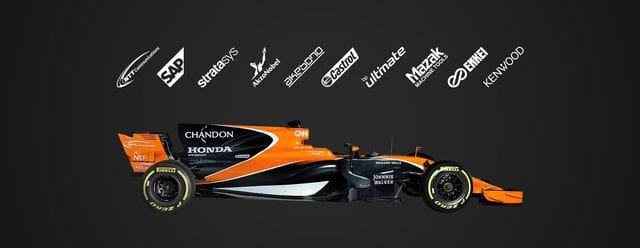
The tech innovators behind the MCL32
Meet our innovation partners who help McLaren Honda keep the show on the road
From 3D printed race-ready parts to high-powered data processing capabilities, find out more about how our technical partners help the MCL32 behind the scenes.
INLINE-MEDIA BIG
NTT Communications
Across a race weekend, we need to share millions of individual data-points, which must criss-cross the globe between factory and racetrack. Our implementation of a cloud-based system has allowed the different departments to share data in a faster, more secure, and more agile way.
At peak times – during a track session – the traffic is immense, so our NTT Communications-supported network must be robust enough to deal with that additional workload, as well as supporting the rest of the business in its daily activities.
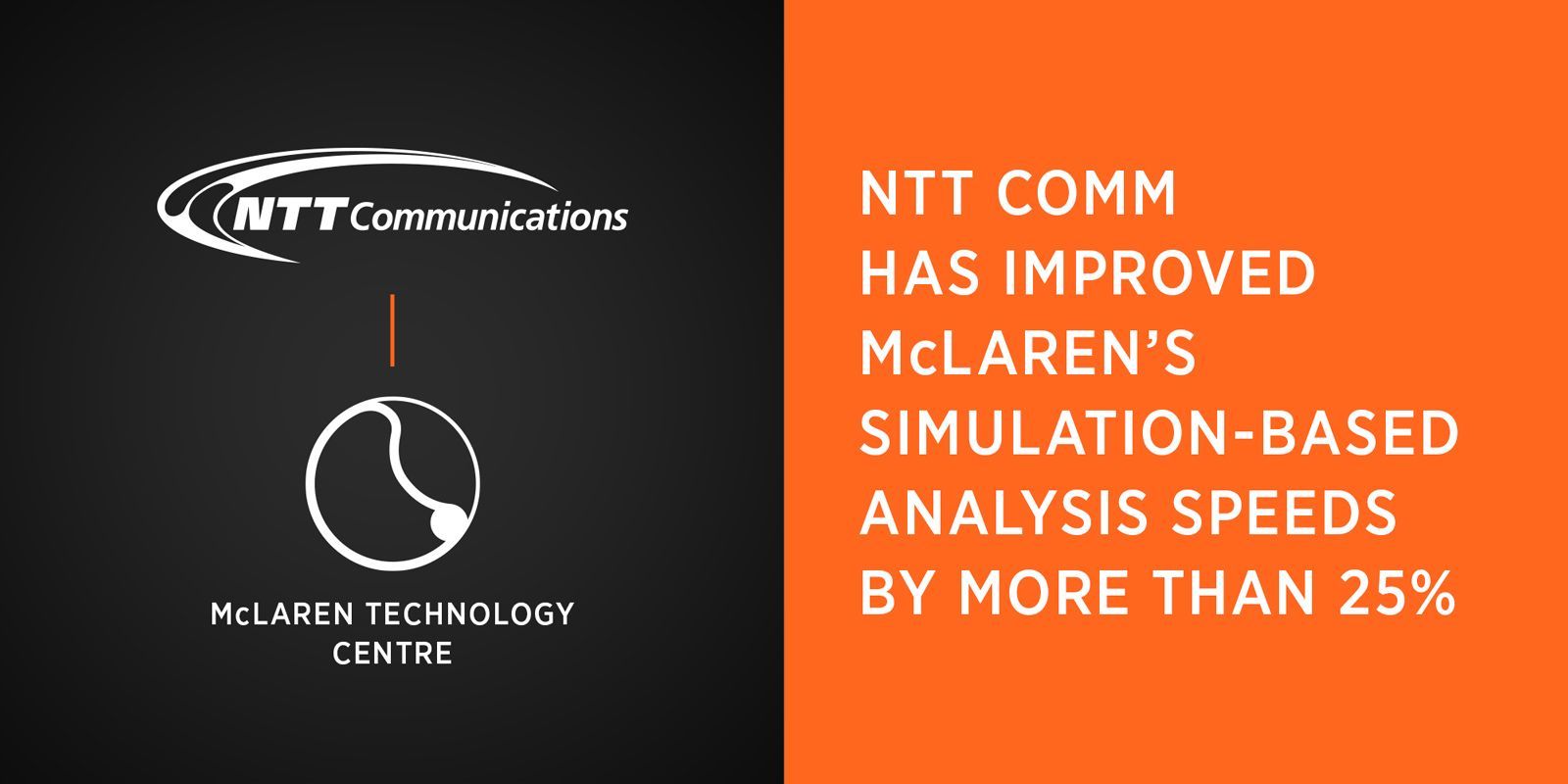
SAP
It makes little sense to collect the data if it can’t be rapidly, processed, analysed and understood. With more than 200 sensors on each of our Formula 1 cars, and millions of data-points collected every weekend, we need to be able to run sub-second analytics using the fastest possible in-memory database. For those operations, we fully rely on SAP HANA.
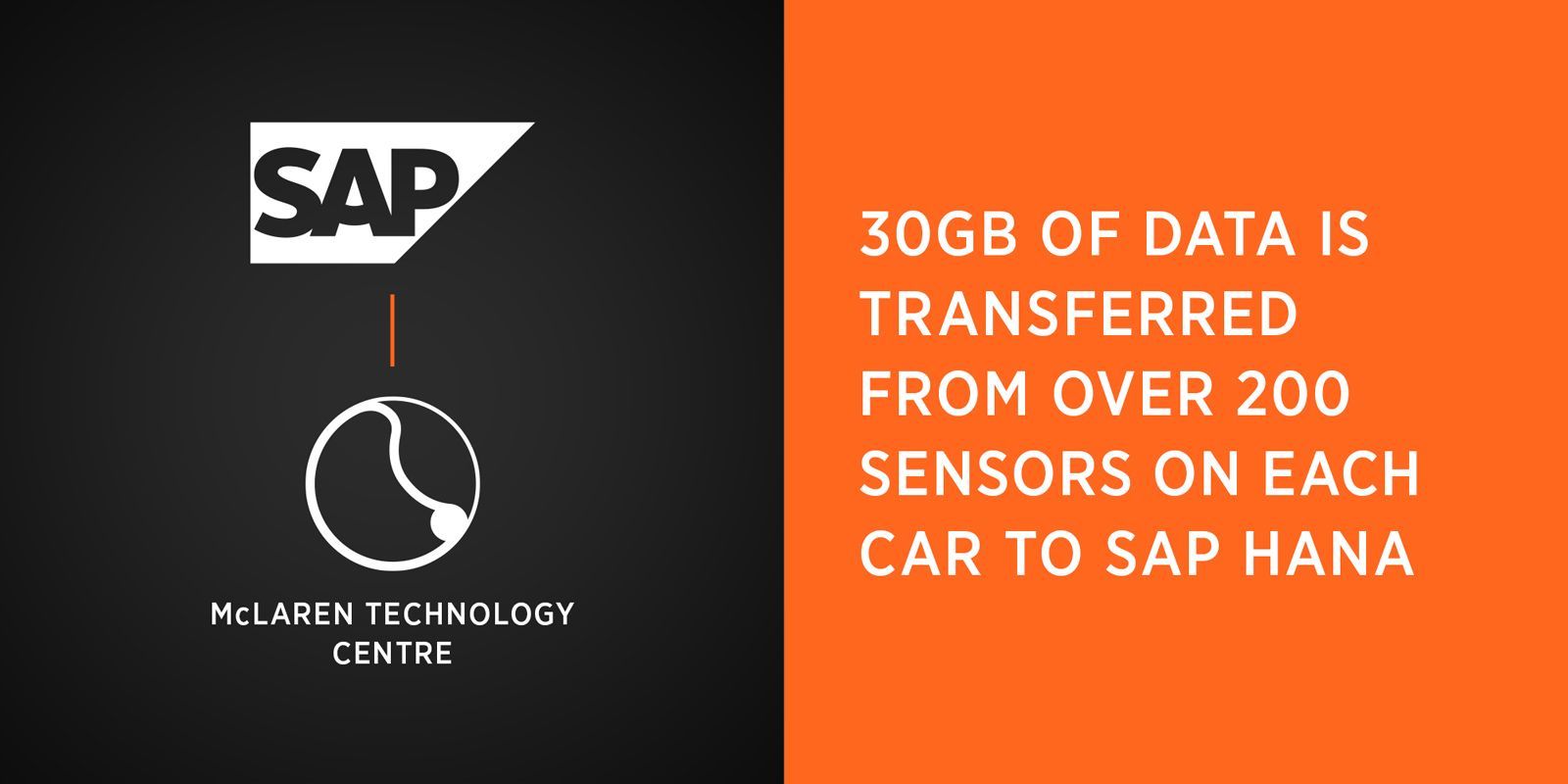
Stratasys
We’ve long employed 3D printers to produce rapid-prototype components for either our race cars or our scale windtunnel models. Now, by using Stratsys’ 3D-printing technologies, we’re actually able to produce parts and tooling for the cars at the racetrack itself. It’s a process that has revolutionised our production capacity, and means we can actually deploy rapid-prototyped components with immediate effect – a massive benefit for our racing effort.
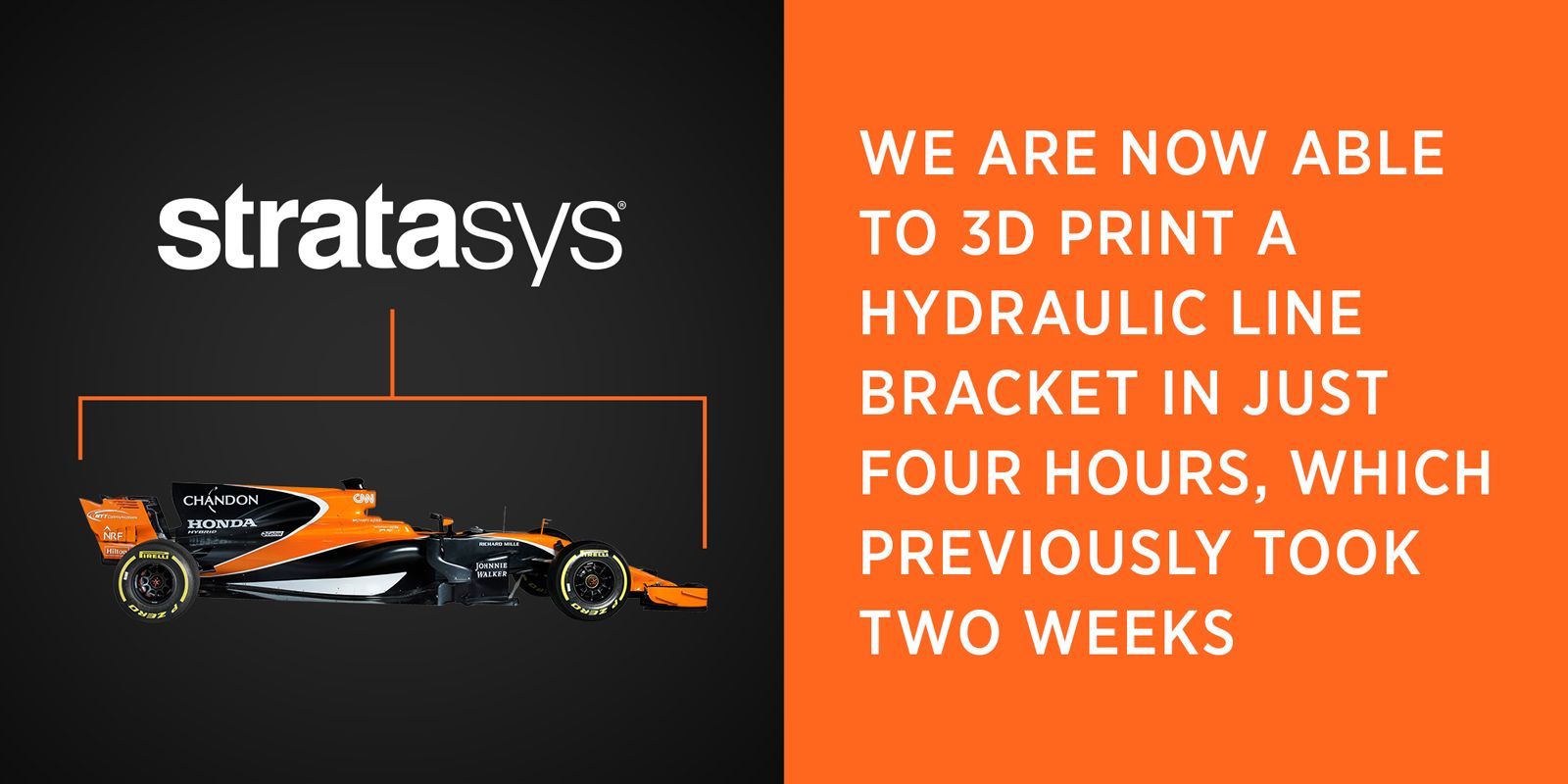
AkzoNobel
Once it’s been moulded, machined, sanded, prepped and primed, it needs to be painted. And this is where we work closely with our paint supplier, AkzoNobel. Together, we’ve created a paint and finishings solution that shaves weight and time from the production process – it cures faster than a regular paint finish and requires fewer coats to achieve the required finish.
Those benefits have also enabled us to significantly reduce the carbon footprint of our paint shop by reducing both energy and emissions.
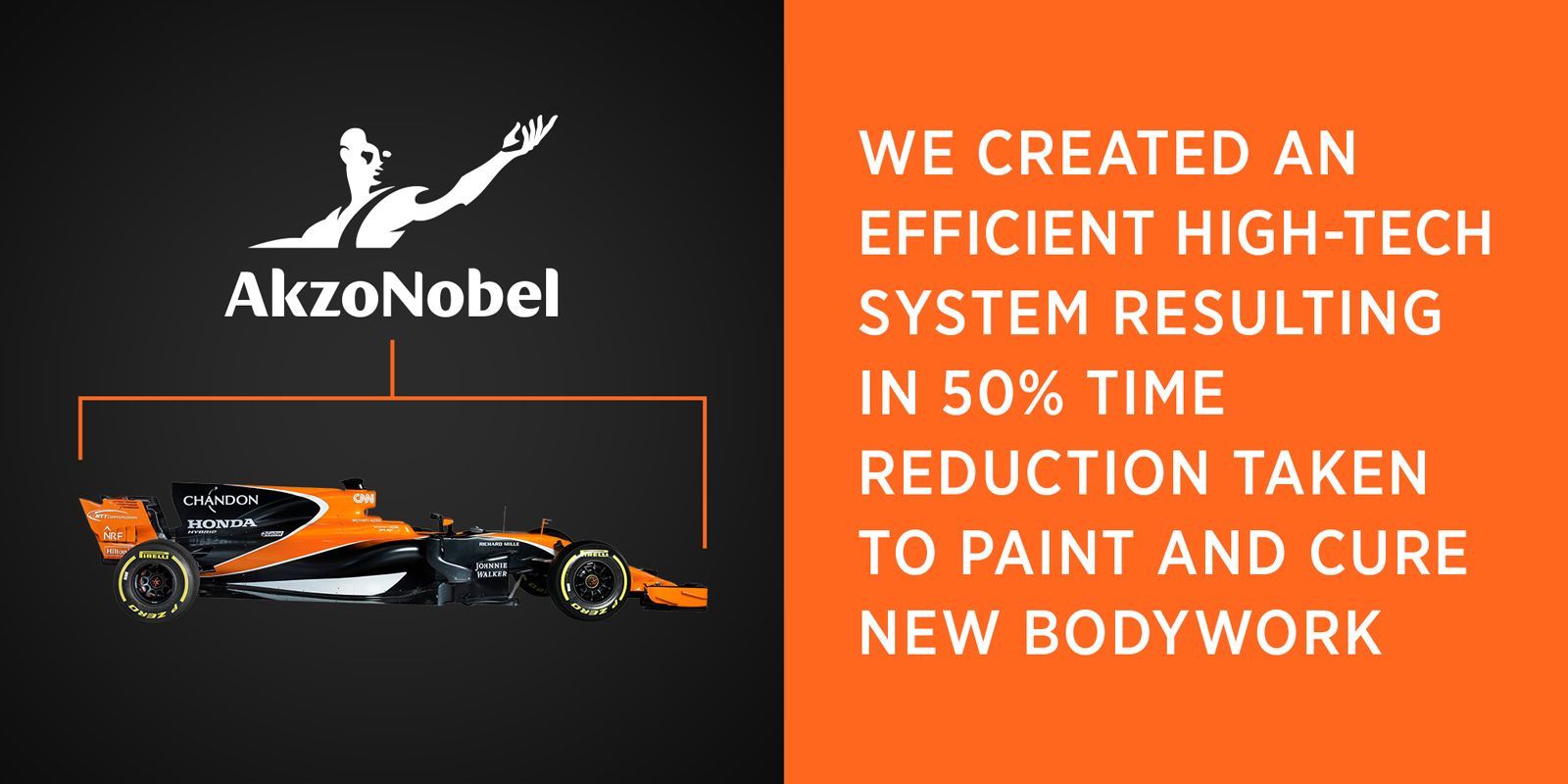
Akebono
It’s hard to even imagine the duty-cycle of a Formula 1 brake system – the Akebono-machined callipers operate at 200⁰C and need to control discs that will glow white-hot at a mind-boggling heat of over 1000⁰C – all while travelling at speeds of over 200mph. What makes it even more incredible is that our brakes remain so robust and reliable – even at tracks like Montreal and Bahrain, two of the most demanding tracks for brakes on the entire F1 calendar.
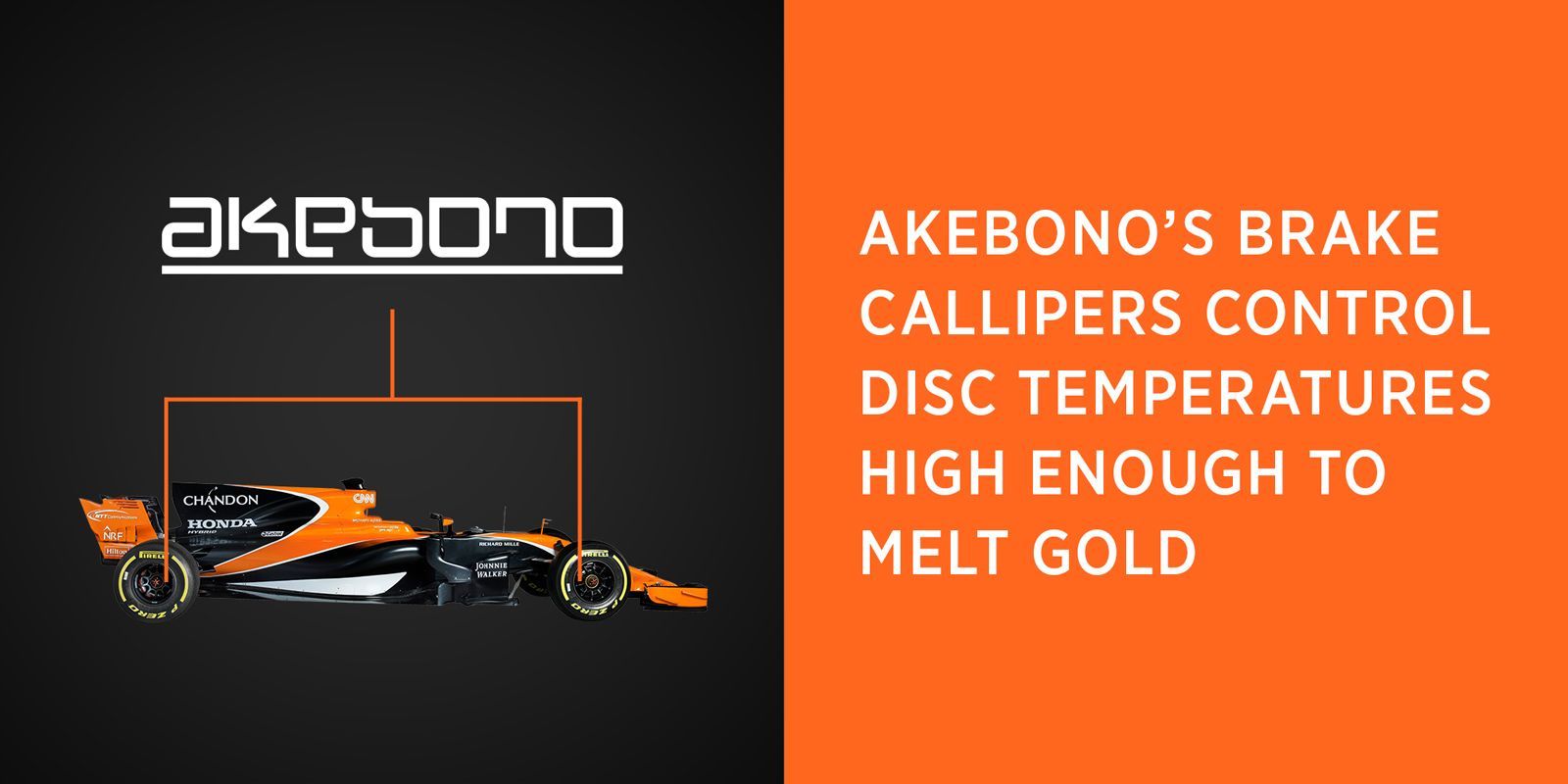
Castrol Lubricant
The oil in our engines and gearboxes is not only essential for the smooth running of these high-tech pieces of technology, it’s also a vital early warning sign for when things might be about to go wrong. By analysing used oil at the trackside, BP’s technicians use a spectrometer that splits light into an array of separate colours based on different particles of wear-metal, indicating any tell-tale signs that could point to a failure.
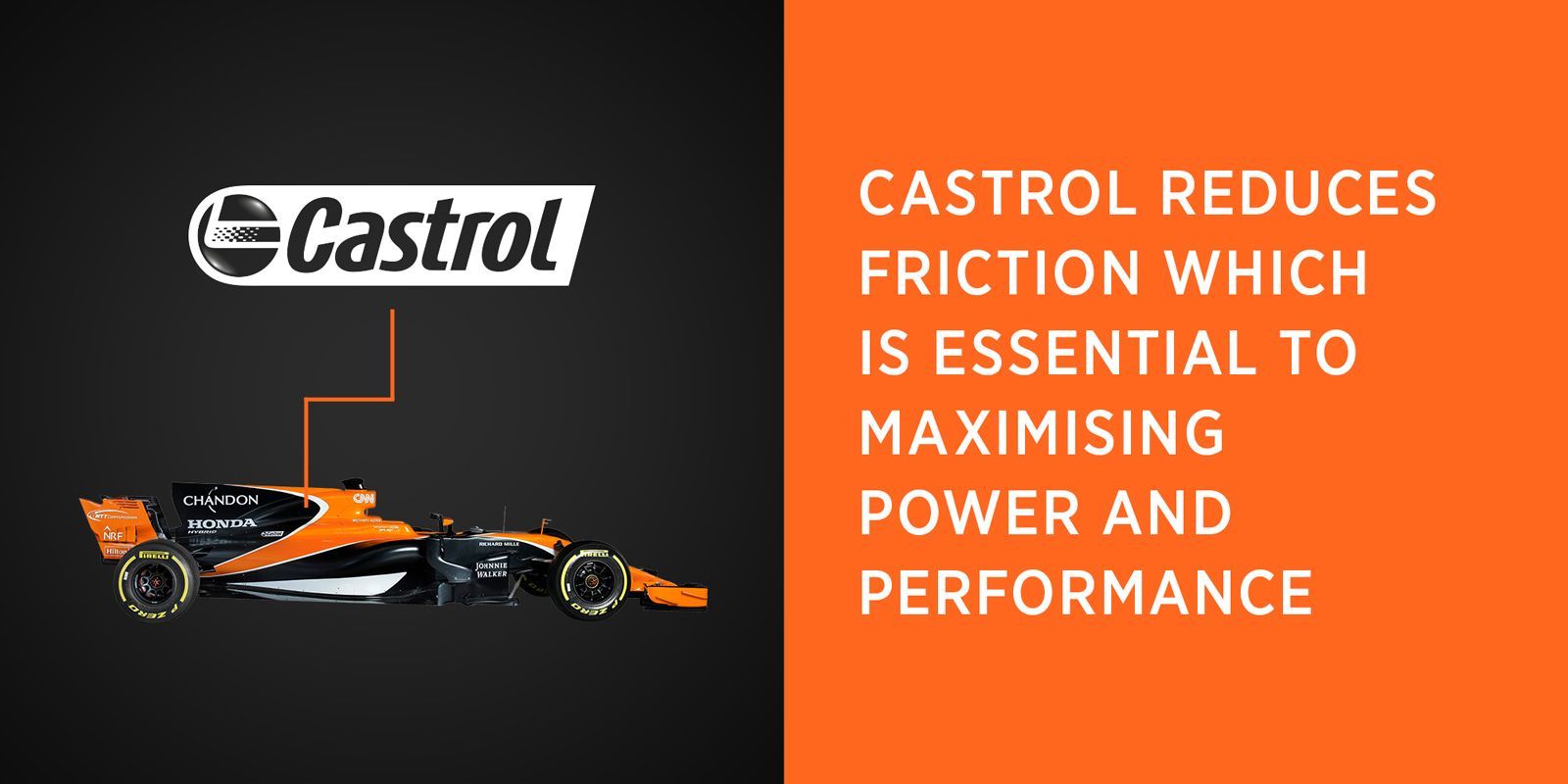
BP Ultimate Fuel
BP’s Ultimate fuel is formulated specially for the team, helping to make a Formula 1 engine the most energy-efficient combustion engine on the planet. F1 fuel needs to be powerful, efficient and low weight – requiring a special formulation that’s developed by BP’s fuel scientists. We’re allowed to develop up to five different formulations of fuel each year.
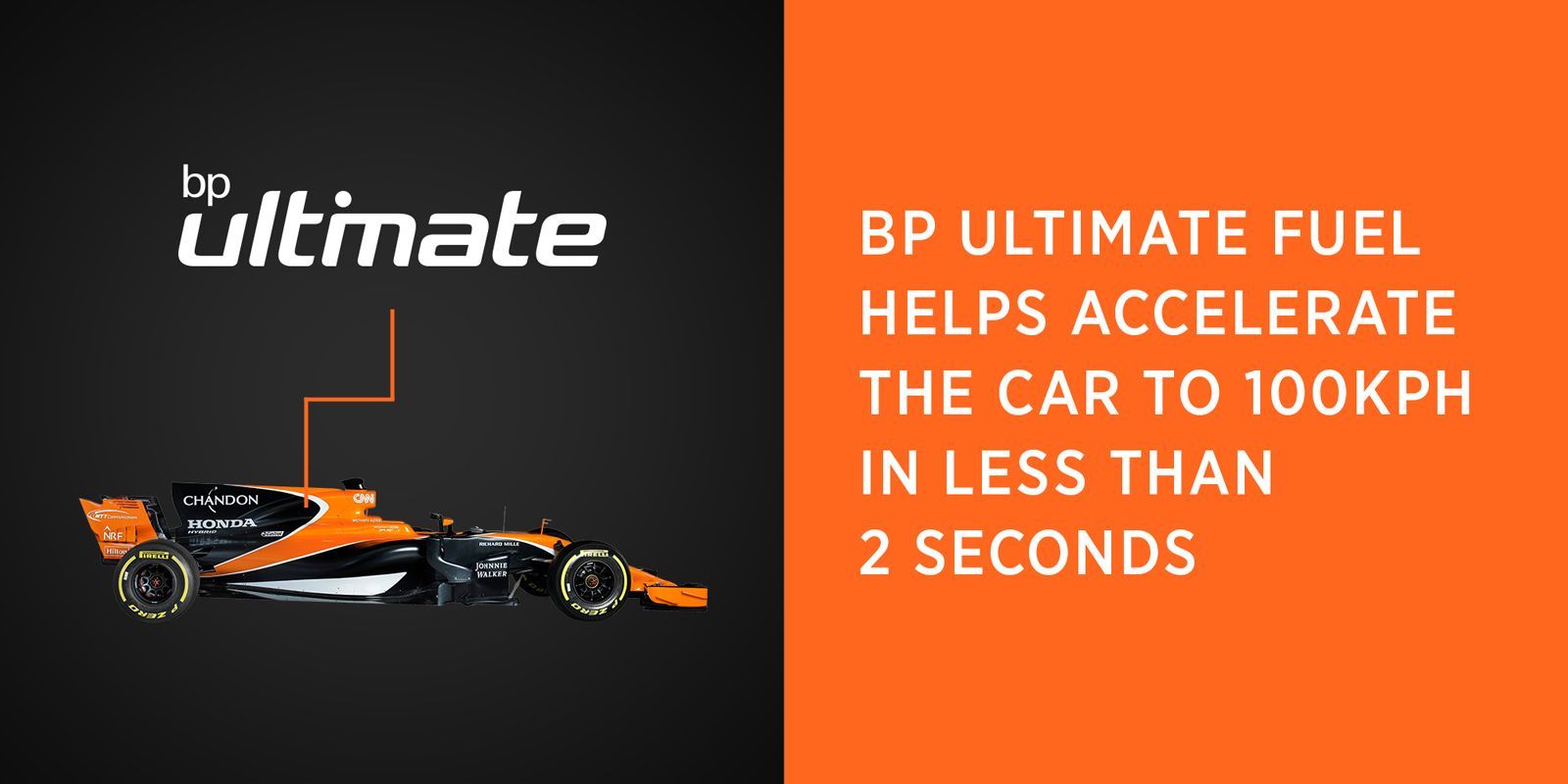
Mazak
It’s overly simple to think of a Formula 1 car as being made from carbon-fibre. It is; but we also use a lot of conventional materials – steel, titanium and aluminium – in our manufacturing process. Our cars comprise more than 22,000 individual components – and more than 4,500 of those are machined in-house by our Mazak machines. They can be relied upon for accuracy: they work to a tolerance of between two and five Microns – that’s less than quarter of the width of a human hair.
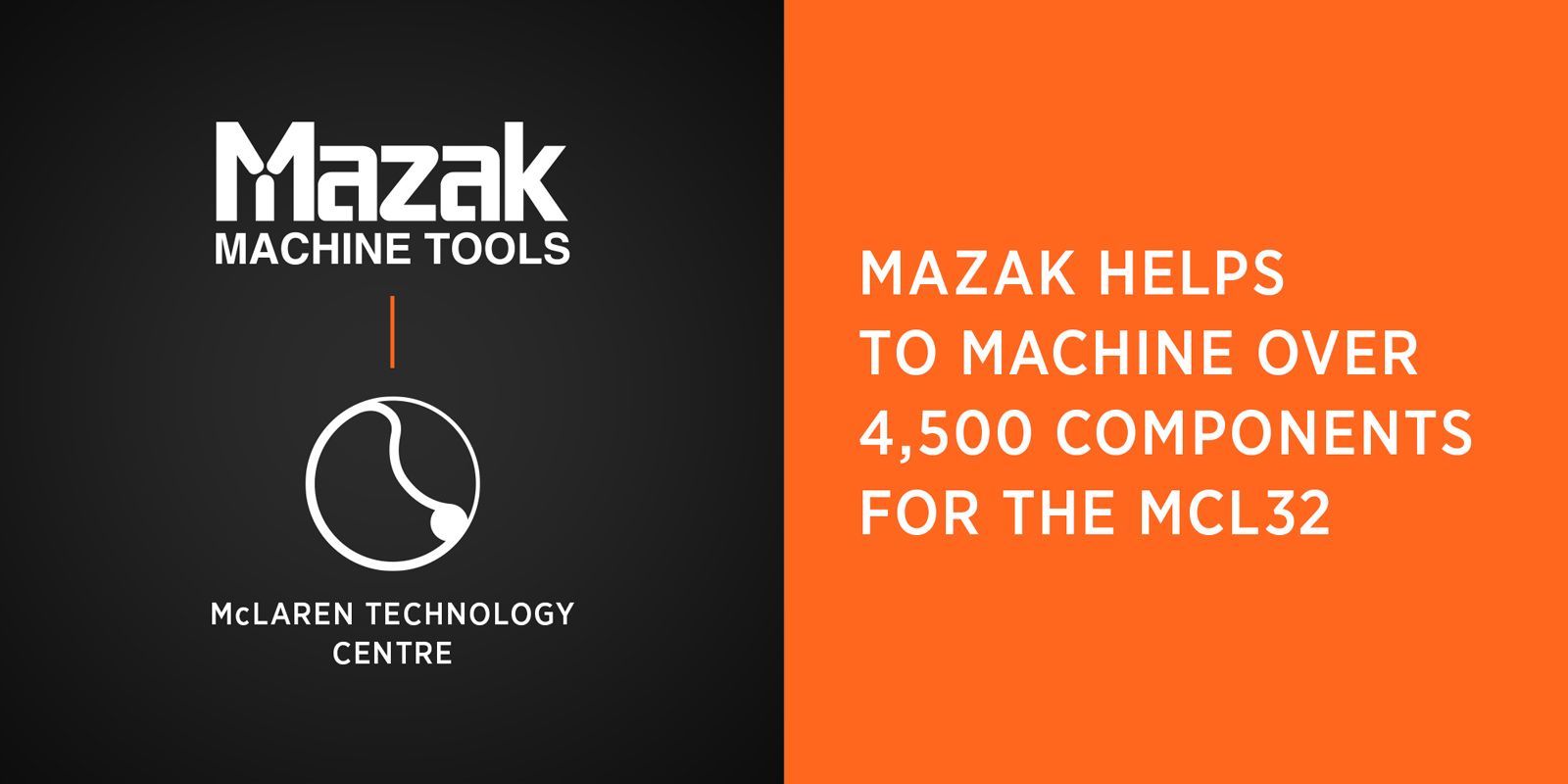
Enkei
In 2017, F1’s wheels became big news – simply because they got, er… bigger. While the new wheels might have made the headlines for their sexier, more retro look, they required some significant beneath-the-hood science to make sure they didn’t become unnecessarily heavy. That meant Enkei’s engineers revising their wheels’ design to find new, lightweight casings, thinner materials and increasingly aerodynamic designs.
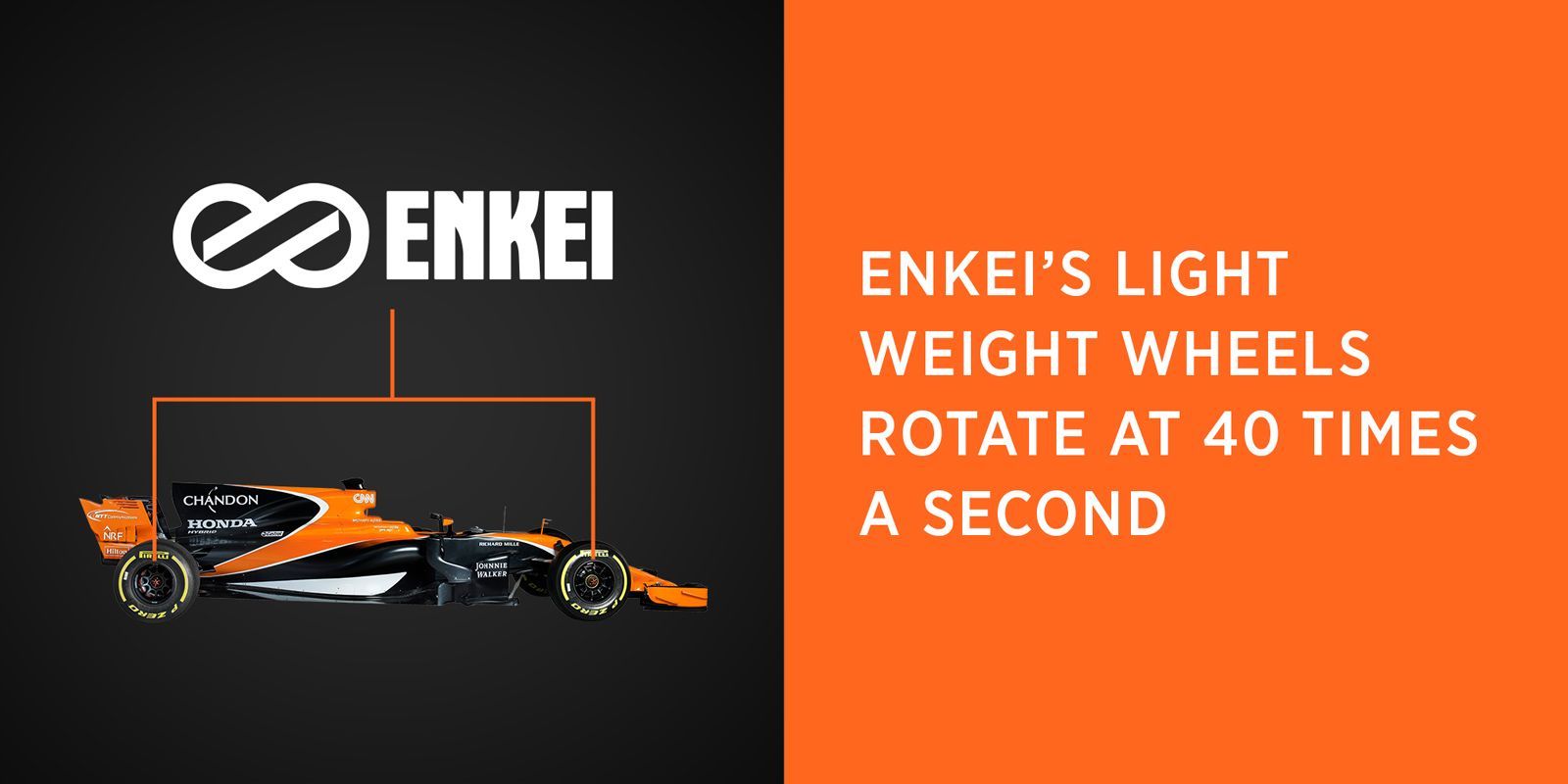
JVCKenwood
Kenwood EXEDGE technology enables the entire team to operate and communicate promptly and clearly in an environment where extreme levels of noise, vibration and impact are the norm. Several frequencies are used to maintain reliable communications during a Grand Prix weekend and the advanced digital technology enables such a high level of security that there is no fear of other teams being able to intercept messages from within the McLaren garage.