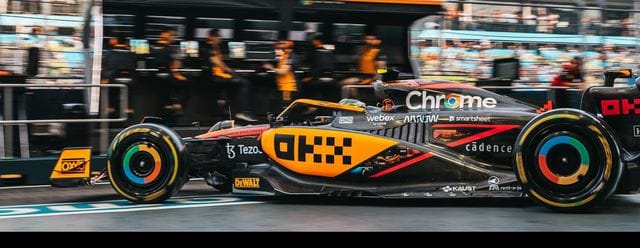
The 'no comfort' approach behind delivering an upgrade – presented by Arrow Electronics
Piers Thynne takes us behind the scenes of the MCL36's most recent package
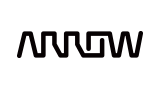
Formula 1 is all about speed. Speed on track, speed of decision making, speed of reactions and speed of development.
The car teams unveil to much fanfare in pre-season isn't the same car that they will finish the season with, and no sooner have the covers come off, is the team already working on upgrade packages for later in the season.
It's an altogether different type of race, but an equally important one: the race to keep up with, and out-develop your rivals.
That race becomes even more critical during a season of significant change. 2022 spawned a new era for Formula 1 with an overhaul in regulations and the introduction of a much tighter cost cap. Andrea Stella, Executive Director, Racing and James Key, Executive Director, Technical F1 described our upgrade programme in reaction to those changes as "aggressive."
Delivery of that work falls under Piers Thynne, Executive Director, Operations. Piers is responsible for the operational strategy of the factory, including project management, quality, manufacture, build, test and logistics. It's a broad remit.
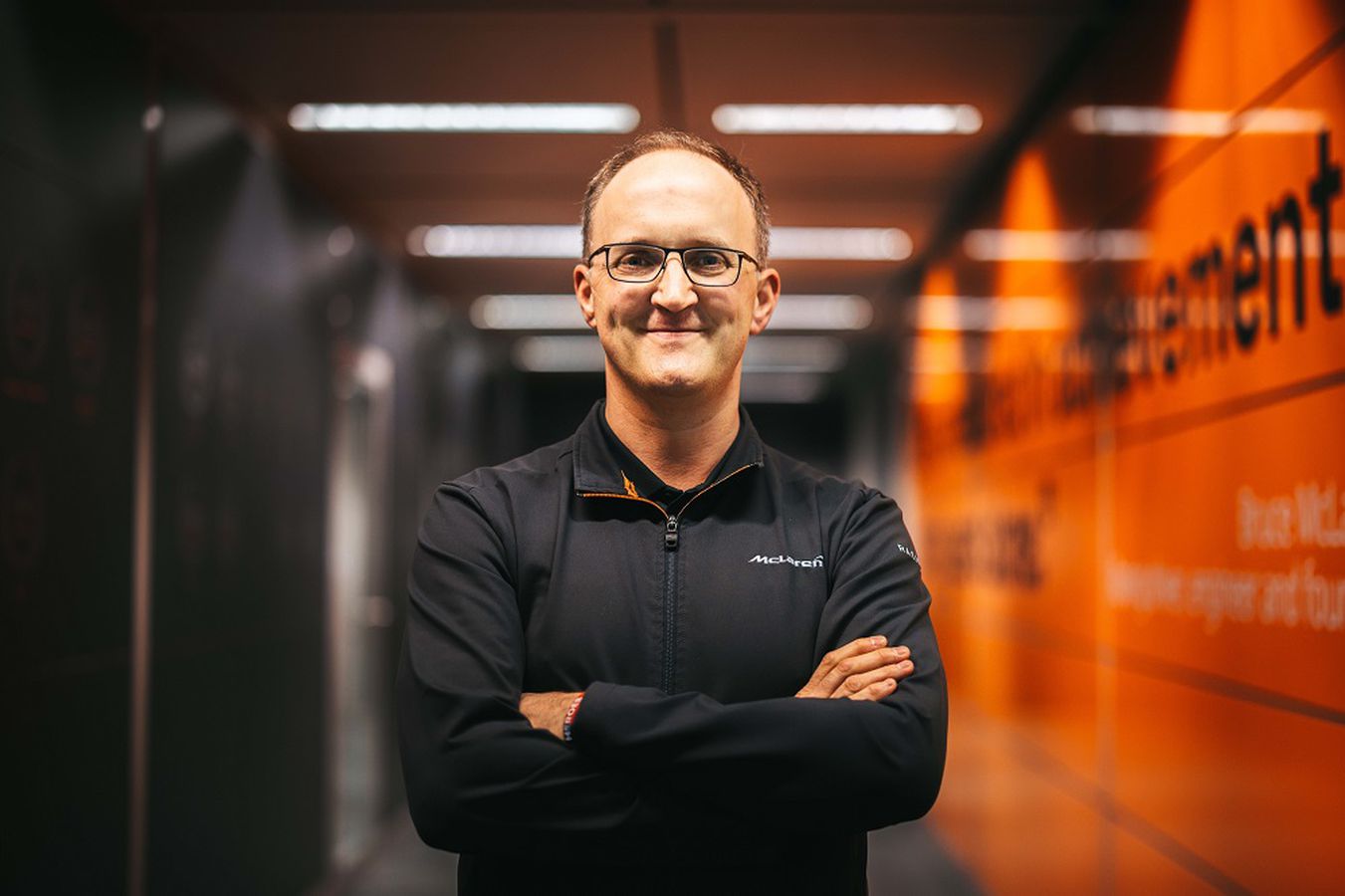
Barely out of a meeting when he joins us for a chat, Piers is speaking on the back of Singapore, Japan, USA and Mexico City where our most recent upgrade - an aero update focused on the floor and bodywork - was put into practice.
The operations team were working on this project, amongst others, before the summer shutdown. Presented by Arrow Electronics, we asked him to take us behind-the-scenes of the MCL36's most recent upgrade and how it was delivered.
"At the start of a project like this, we first try to understand the scope in detail," he says. "Then, we create an aggressive plan and see where it lands, and the data gives you a clear steer on this”
"In June and July, we were in aerodynamic development, and it started to show enough promise for us to create more detail on this from a planning perspective. We spent a lot of time in July making sure that the performance step was enough because the scope of work and cost was high. The operational side of the team was going into a lot of detail to be certain and de-risk all aspects because the scope of work was so vast, and it involved taking the chassis out of service.
"This was a bonded chassis change, so we take the chassis back to its raw state and re-bond the brackets, the radiator ducts, the side pod uppers and everything else back on it. It was a considerable effort, and like everything we do, it's all about collaboration and teamwork."
It's a common misconception that upgrades are aimed at delivering short-term speed. While this can sometimes be the case, they more regularly focus on the mid-to-long term. Our most recent update was aimed at maximising our current package over the remainder of the season whilst allowing us to learn as much as possible for the development of next season's car.
That level of forward-thinking is ambitious but achievable. It can only be realised with the level of corroboration and communication Piers is referring to.
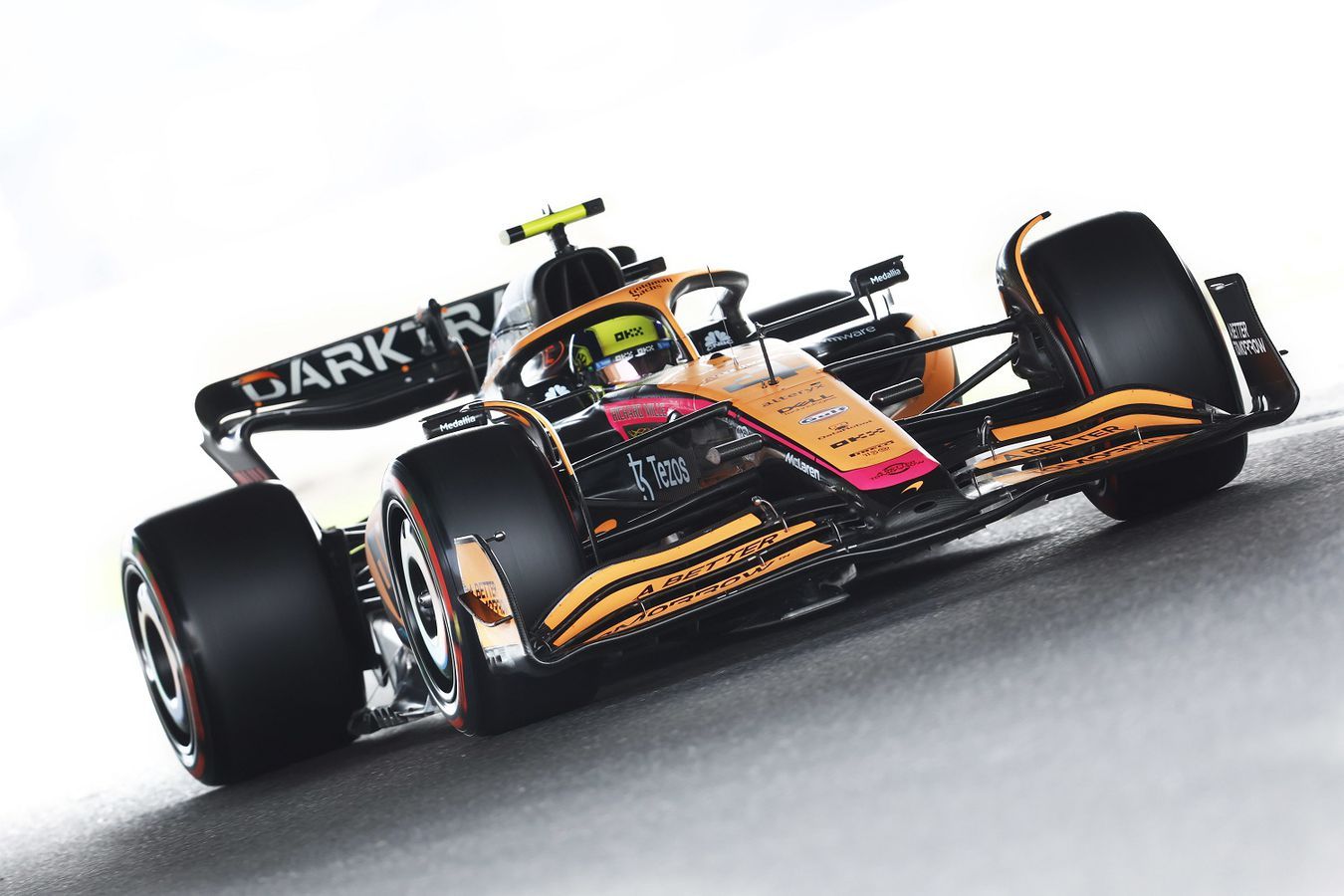
A vast array of people and teams are involved in the process. An ability to make a highly complex plan with as much “concurrent activity” as possible clearly can be a difference-maker when working to such fine margins. "The project management team did this excellently – giving as much time as possible upstream," Piers reiterates.
"They synchronised everything so that it happened in the right order and as late as possible. The design team had a lot to do in a very, very short space of time, as did the operations team. The approach needed to be very clear and very sensible. Everything has to be done in the right order, including all of the manufacturing tasks and the pre-fit."
The team use the factory as much as possible, but where necessary, they source and purchase items to ensure the project remains on track and can be completed in the required timeframe. None of this is done on a whim, though, it is all planned and costed in advance.
Getting the timings right can be the difference between building the car at the McLaren Technology Centre in controlled, comfortable conditions, to putting it together in a hot and humid garage in Singapore.
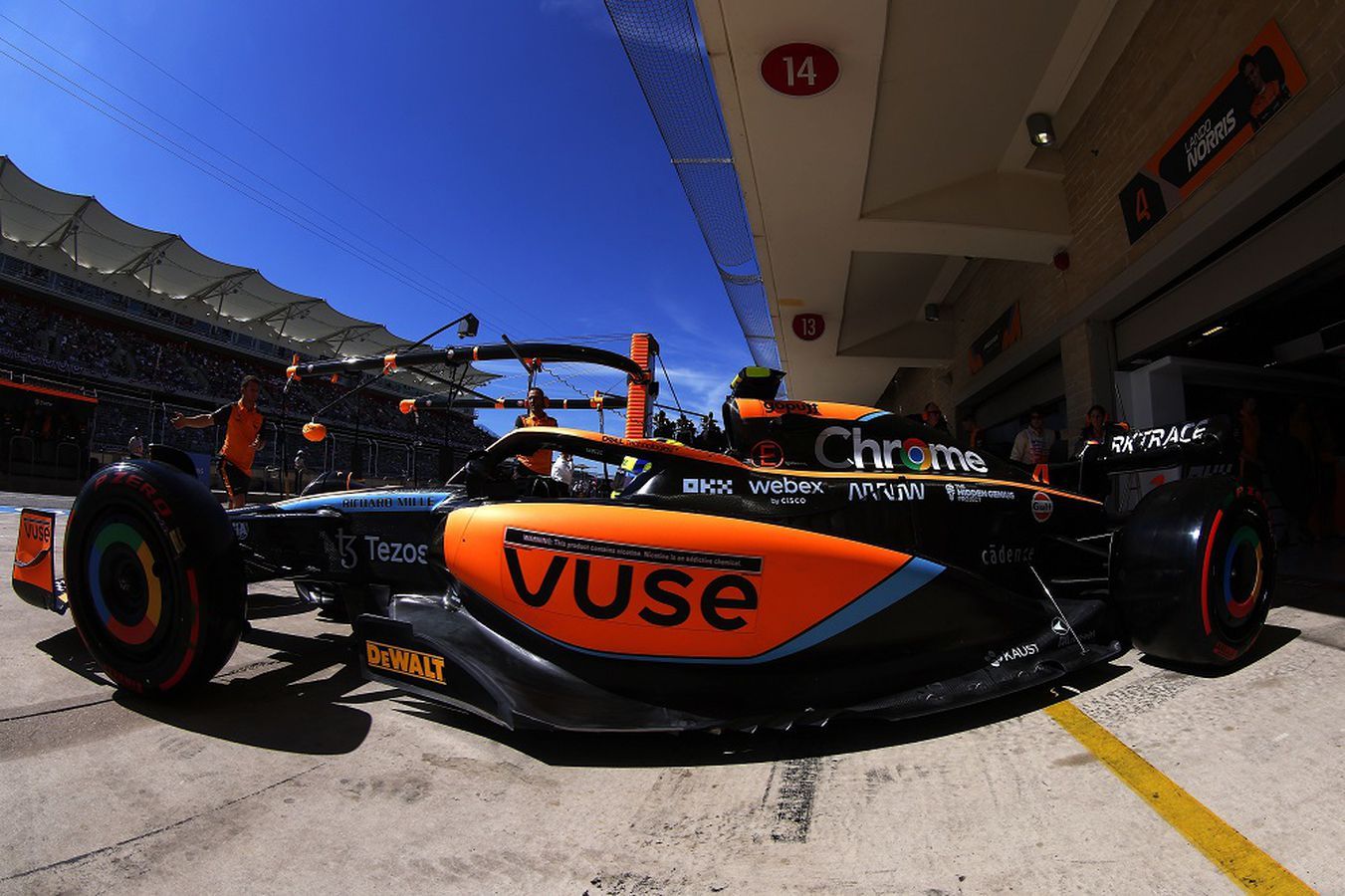
"That was a key aspect," Piers continues. "You need to deploy an upgrade of this volume with checks that list all of the risks and the key information to ensure a seamless rollout. Bar a few niggles I'm pleased to share that's what happened.
"What we don't ever have to do is fight the comfort factor, no one ever says that they want to make a project easy. If someone says four days, I'll ask, 'why not three and a half?' Or if it's two days, I'll say, 'I know we can do that in a shift'.
"Part of my role is to inject some healthy challenge and make sure that we are using the flexibility of our factory and supply chain to get additional performance to the track at the earliest opportunity."
The travelling team who worked with the upgrades in Singapore and Japan were a key part of the process. As the ones working with the cars on the ground, their input in each stage of development can vastly lessen the risk when the cars get to the track.
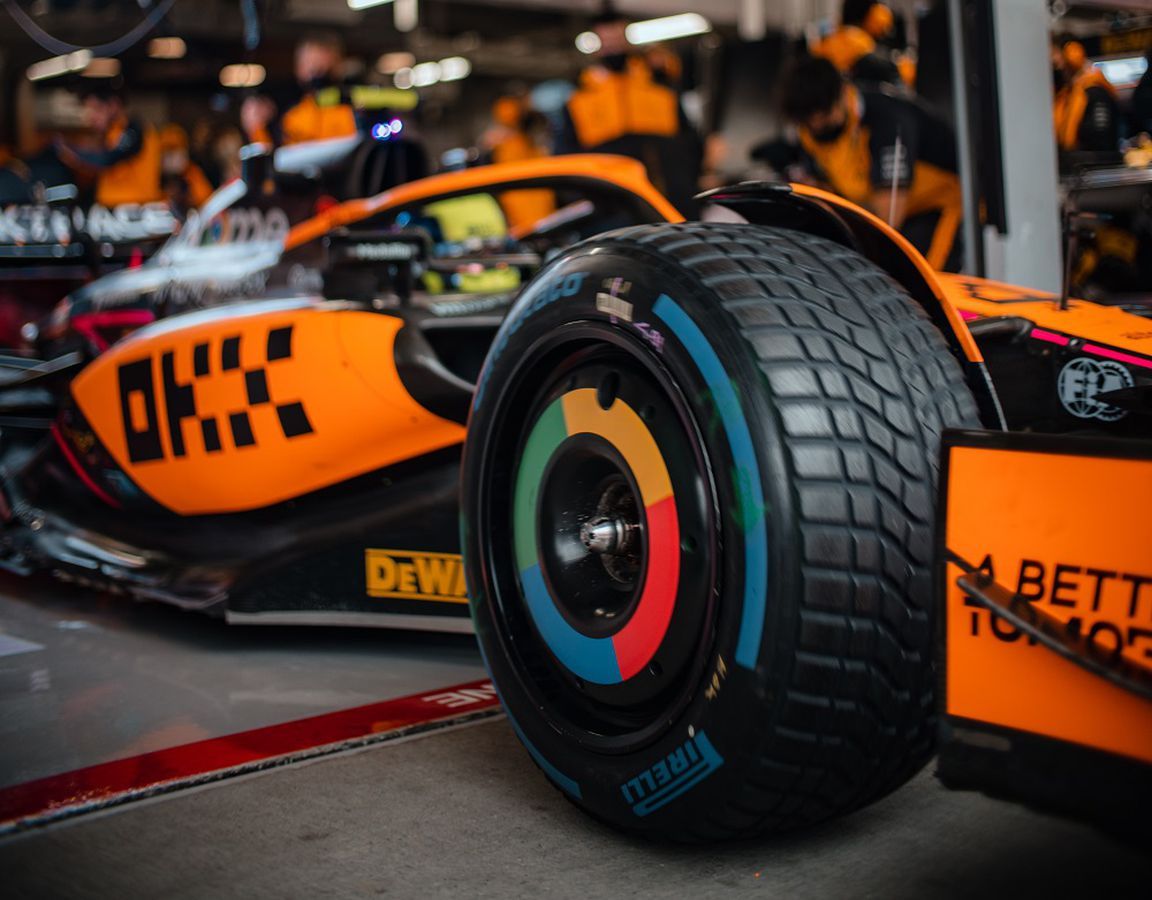
"Their experience is invaluable, they will listen and watch to make sure that everything is thought about, considered and factored in," Piers explains. "They will also drop in golden nuggets of information that are really helpful. For example, after a conversation with them, we pre-fitted all of the pit equipment that interfaces with the car."
The size of the upgrade was of a similar scale to the ones delivered in France and Spain, but unlike those projects, this was to be delivered at a flyaway event, with September's Italian Grand Prix marking the end of the European season.
A journey in a truck is much more risk-averse than a long-haul flight. It was partly for this reason that the team delivered the upgrades separately, one on Lando's car in Singapore and the other on Daniel's car in Japan.
"There is a difference between running an upgrade that's going to a European race and running an upgrade that's going to the other side of the world," Piers continues. "Some significant unseen architectural changes were also embedded into this project."
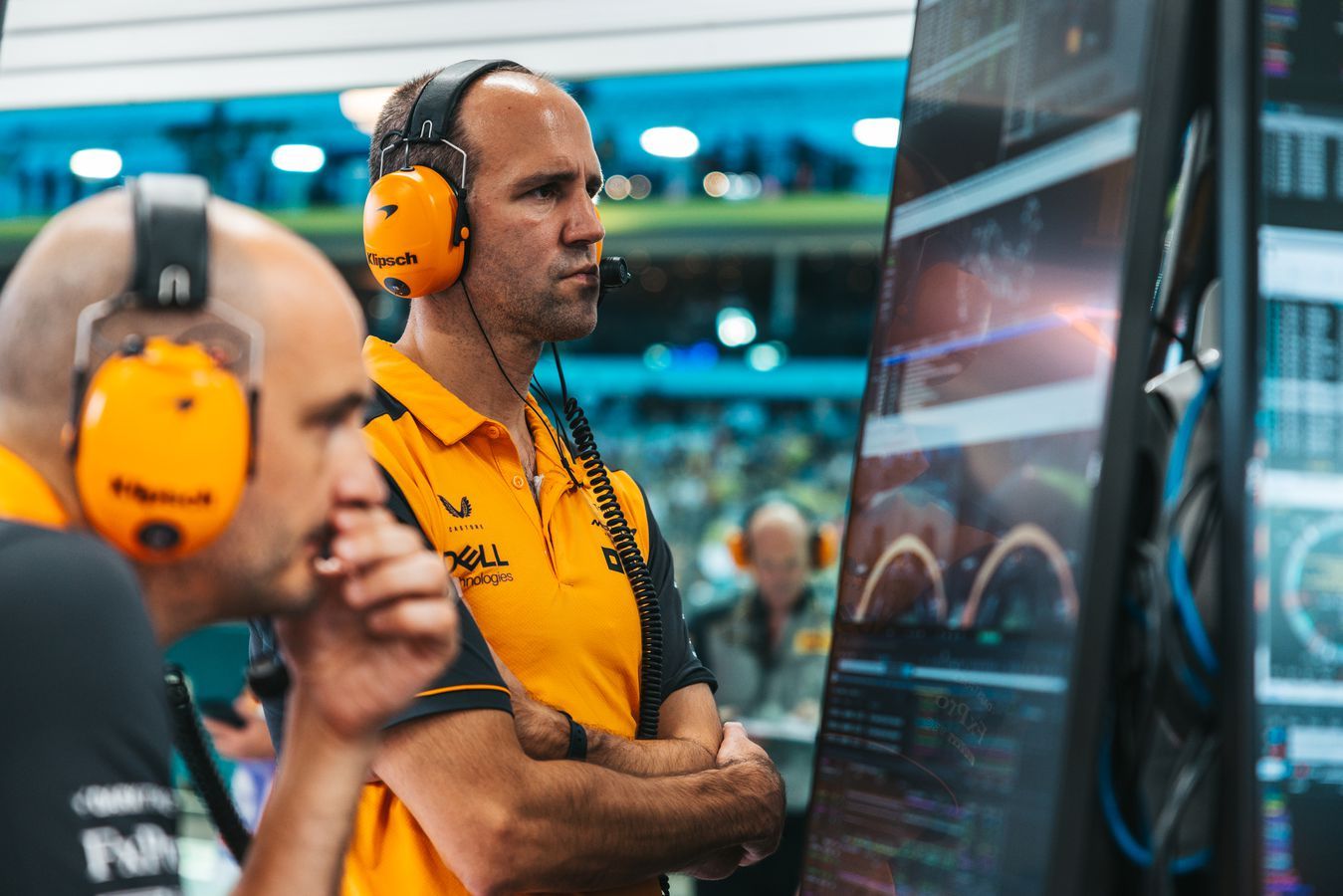
"For those reasons, and the logistics of taking a chassis out of service, we needed to balance risk differently, so the right answer was to deliver one at a time. And we rolled it out with very, very minimal issues. It was a considerable effort, and like everything we do, it's all about collaboration and teamwork."
As well as the effort and risk involved, upgrades are costly and with a strict financial cap now in place, extracting as much value and performance from them as possible has become even more important.
The margin for error is practically non-existent. There is no 'second attempt, we go again', because, financially, there isn't the wiggle room to do this. You either get it right, or you switch the focus of the next upgrade. However, small changes can be made to make meeting the cost cap easier, as Piers explains.
"Under the cap, we've taken different approaches," he says. "For example, we have tried to be very lean on spares. In general, with the cap, you have to take a slightly different approach to risk – you have to sign up for the risk and go in eyes wide open. And that's an honest, joined-up discussion I have with James and Andrea.
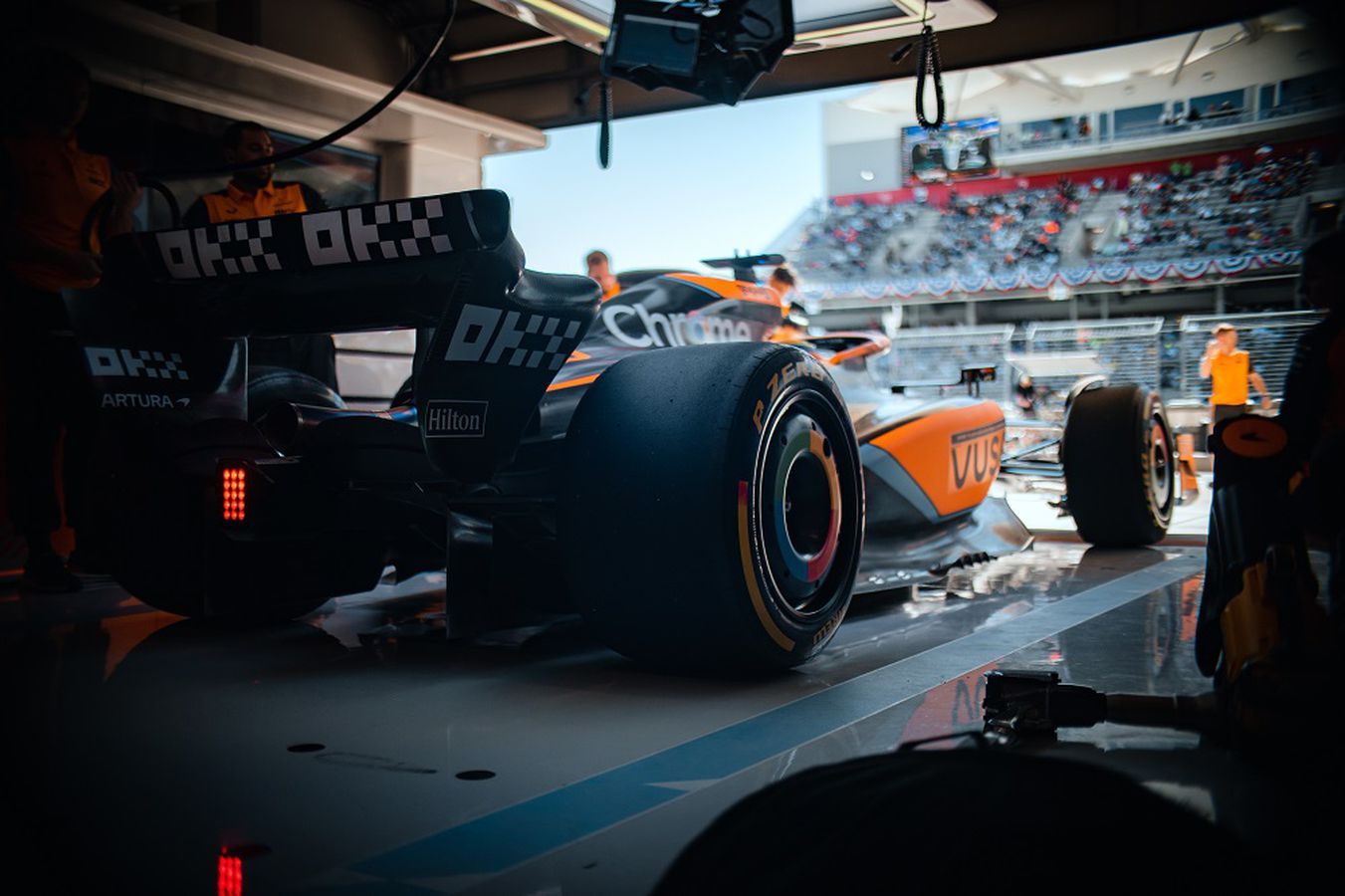
"For example, I might say I can only get them two of a part, and then it is up to Andrea whether the potential reward is worth the risk of only having two."
With the upgrade now installed, the team believes that dry conditions will allow us to learn more about how to optimise the car, with weather conditions in Singapore and Japan minimising the data gathered.
Back on the factory floor, multiple plates continue to be spun, and work on next year's car is well underway. However, Piers believes that his team can take a sense of satisfaction from an upgrade successfully delivered.
"The quantity, quality of build and aero care of upgrades we've delivered through work from all areas of the business, from the factory, to transport and logistics, has been fantastic this year. It's been a real team effort, but we continue to strive for more marginal gains.
"Now, we are looking forward to a bit of a focus shift to the winter build and new concepts, which is starting to hit the factory and workshops now."
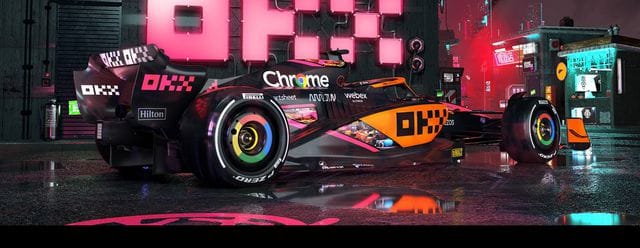
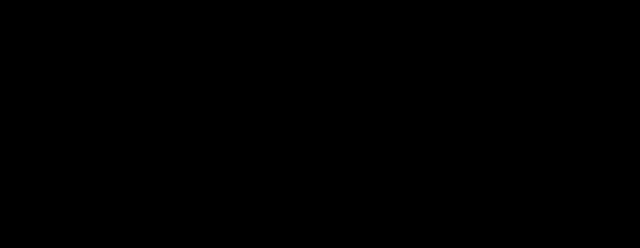
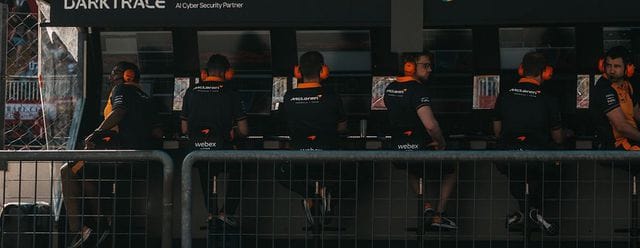
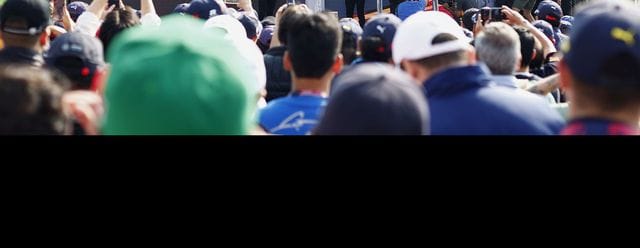
Downtown Tokyo X Downtown Woking: How we created the "Future Mode" livery
We spoke to the McLaren Creative in-house design team to get the lowdown on how they created the OKX "Future Mode" livery that will feature on the MCL36 at the Formula 1 Singapore and Japanese Grands Prix
Getting ready for '36
New technical regs, a cost-cap and covid-19 mean building the MCL36 is not business as usual
A new era, six months on
McLaren Racing's Andrea Stella and James Key discuss the new Formula 1 regulations, the 2022 season so far, and the remaining races
That was the weekend that was
Read the story of the Mexico City Grand Prix according to social media – aka McLaren Racing fans.
Join the team
McLaren Plus is our free-to-join fan loyalty programme, bringing McLaren fans closer to the team with the most inclusive, rewarding and open-to-all fan programmes in motorsport.
Sign up now, or current members can amend their details in the form below if necessary.